Part 4 of Our Owner-Builder FIRE Journey Series
Man, I can’t believe Christmas was less than two months ago. January was such a looooong month for us. We’ve made so much progress on this construction. Oh my lord! I don’t even know where to begin, so let me go through our photo journey and take it from there.
From our previous post, the last step we completed was pouring the slab on December 31st. We let the slab rest for a couple of days. We couldn’t get materials in until early morning on January 3rd. Even though Ivan, the “block guy,” and his crew weren’t scheduled to start on Saturday, January 4th, they showed up an hour after the materials arrived and started working on the exterior concrete walls right away.
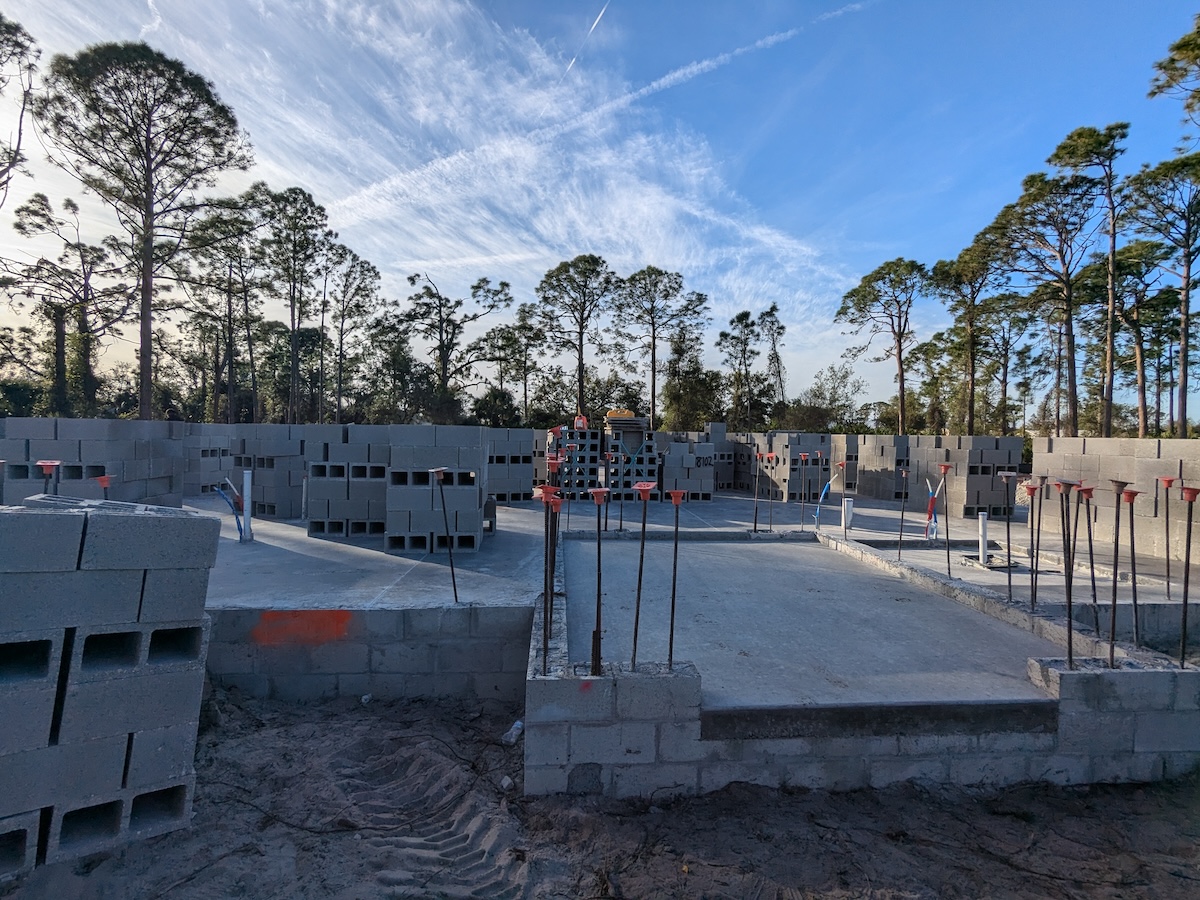
This phase of construction is crazy hectic, and I found myself showing up at the job site at least every two hours to make sure things were going smoothly and no obvious mistakes were made. Since the workers showed up unexpectedly a day early, Russell, our shell contractor, couldn’t make it. No big deal since the guys knew what they were doing, and I felt comfortable looking out for the job. I was just happy to start earlier and not have any delays.

When Things Go Wrong (And They Will)
Wanna know what makes custom home building interesting?
The mistakes.
Were mistakes made?
You bet! LOL.
Never a dull moment when it comes to construction. I was warned by Russell, during the design stage, that this is a big house, and some mistakes will happen along the way. From the minute you break ground until the interior walls are built, are the most critical times because if you, as an owner-builder, disappear for a few hours or a day, it’s hard to correct some mistakes. I’m glad we live only a few minutes’ walk from the property—I can swing by anytime and usually catch mistakes quickly.
Pro Tip: In custom home building, production crews are used to cookie-cutter homes. Your unique features require extra attention, so plan to be on-site frequently during critical phases. Those two-hour check-ins might seem excessive, but they’re much cheaper than fixing mistakes after the fact.
The Case of the Vanishing Space
A big mistake that happened on the fourth day of building the walls was caught by my wife on video. I took a video of the walls, and almost at the end of the video, she noticed that a skinny worker was the only one standing between the two windows of our bedroom!
Why was this problematic?
Well, these two windows are supposed to have enough space to fit a king-size bed between them. These are tall, skinny windows (24×62), which are perfect to align with two nightstands. When you can barely fit a person between two windows that are supposed to have room for a king-sized bed, you know something’s wrong!
Tatiana spotted this and said, “Go back over there immediately!”
When I got back to the site with Tatiana following shortly after, I went over the plans with Ivan to see where we went wrong. Well, he was viewing the blueprints on his phone while holding it flat, and when he was measuring, he thought a 9′ distance between the windows was a 6′ distance. Even though the foot measurement symbol should’ve given it away. Anyway, we caught that mistake. The mortar hadn’t settled, so they brought it down and redid it. There wasn’t much material waste (there was extra mortar, and they reused the blocks), just some lost time and no additional charge to us.
Pro Tip: When reviewing construction progress, video documentation is worth its weight in gold. Take videos walking through the space daily, even if things look correct at first glance. Having a second set of eyes review the footage (thanks, spouse!) can catch issues you might miss on-site.

The Honest Contractor Award
Speaking of quality control, here’s another story that proves the value of working with honest contractors. On the last day of block framing, I made my routine site visit expecting to see the completed right front wall. What I didn’t expect was to find a previously built back wall completely dismantled and workers cutting into the slab!
My heart skipped a beat, and I immediately reached out to Russell to find out what was happening. Turns out, during the initial slab pour, one corner had been measured incorrectly, making it two inches longer than it should have been. Rather than try to hide this discrepancy or work around it, the team took the initiative to fix it properly. They deconstructed the affected wall, trimmed those extra inches off the slab, and rebuilt everything to exact specifications.
The fix cost us a few hours of work, but Russell’s transparency about the issue spoke volumes about his character. In an industry where it’s tempting to cut corners or hide mistakes, having a contractor who prioritizes doing things right is worth their weight in gold. Once the wall was rebuilt correctly, we had all the walls perfectly aligned.
The Effing “Fortress”
After completing the walls, we awaited our inspection, with Russell spending the entire morning on site. The inspector finally arrived around 1 PM, gave the structure a quick once-over, and was nearly out the door, or lot, when Russell stopped him.
“Aren’t you going to check that all cells have rebar according to the plans?” Russell asked.
The inspector’s response was memorable: “What for? You’re building an effing fortress here!”

Still, Russell wanted to be thorough and asked me to verify that this was indeed our official inspection and that we’d passed in the system. We had—with flying colors. The inspector’s colorful comment was actually quite a compliment, confirming that our construction was more than adequately reinforced.
After the inspection, another team came in to fill in the cells solid with 17 yards of concrete and install the straps that would attach to the trusses.

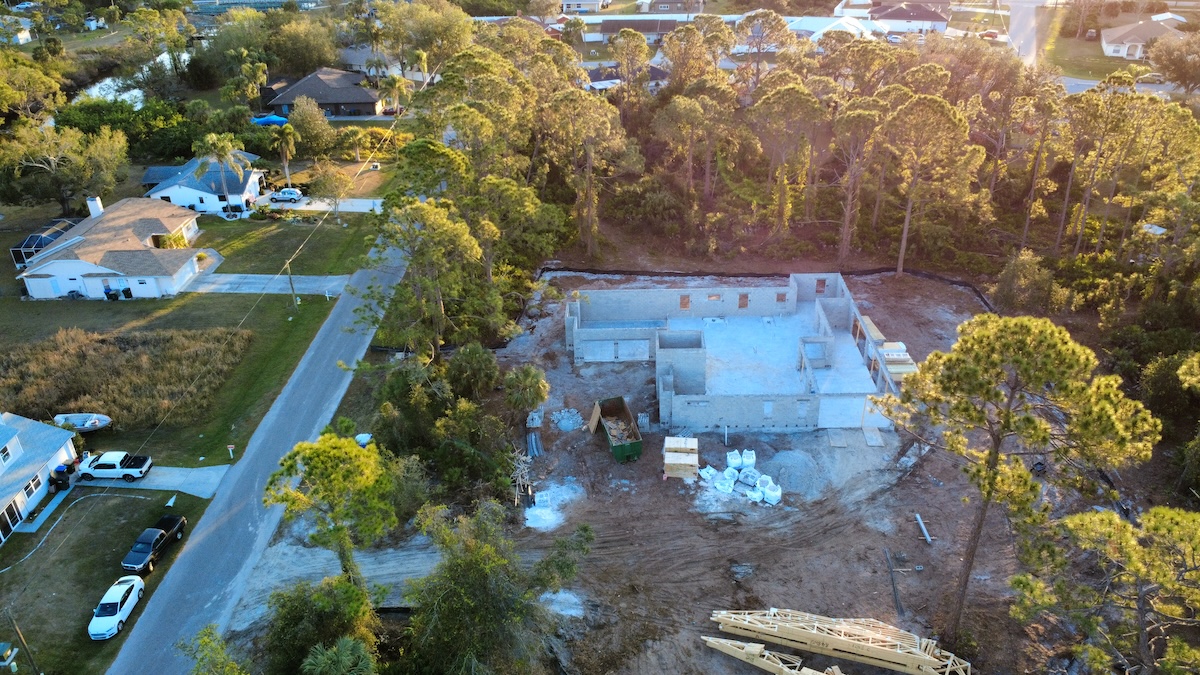
Roof and Interior Wood Framing
Next up was interior framing, trusses, and the roof deck. We brought in Mariachi’s crew for this phase–and no, we didn’t hire a Mexican band for construction. Or did we? Mariachi is actually the nickname and company name of our framing contractor as he used to be in a Mariachi band. I discovered him during my reconnaissance missions a year ago, watching various construction sites in action. He was framing a house when I approached him for his contact information, and as a bonus, he connected me with Russell, the shell contractor who handled our block work.


The lumber and trusses arrived right on schedule on January 9th. The crew’s first priority was constructing the load-bearing walls to support the trusses. With the roof deck and trusses in place, we immediately coordinated with the roofing company for the underlayment installation. With rain forecasted for Sunday, we pushed hard to complete most of the underlayment that Saturday.
Once the roof was secure, we moved on to framing the interior walls. This is where things got interesting – actually walking through the spaces gave us a whole new perspective on the layout. The beauty of being owner-builders meant we had the flexibility to make adjustments, and we definitely took advantage of that!
We completely reimagined the master bedroom entrance, finding a way to eliminate a door while maintaining privacy through clever design. We also noticed the hallway leading to the girls’ rooms was unnecessarily wide at 5 feet. By reducing it to 4 feet, we gained valuable extra space for both the office and laundry room.
Speaking of the office… well, this is where we encountered one of our more memorable “learning opportunities as you’ll soon find out.”
The Office Ceiling Drama
We made a big office boo-boo. Just take a look at the trusses in our office photos below.


Yes, those trusses were protruding through the office window. Here’s what happened: When proofs for the trusses came in during the design process, the entire house had a 10 ft ceiling. I noticed the office windows seemed too high for a 10 ft ceiling and asked the architect to confirm the height for that particular room. The truss company was asking for a confirmation on that truss height as well. This was back in December 2023.
Long story short—we confirmed a 13 ft ceiling with the architect, but somehow that detail got lost in the shuffle. The proof for the trusses went out with everything at 10 ft. ceilings!
So there I am, panicking.
What do we do now?
Cover the top window with blocks and forget about it? But then what about the window we already bought?
Plus, the front wouldn’t look right without it, as the bottom window wouldn’t align with the rest. After bouncing some ideas off Russell, we reached out to the truss company for repair drawings. They came through with engineer-sealed plans and didn’t even charge us, probably because they realized that they partly dropped the ball on this. I did send them an email confirming the ceiling height back in March 2024, but the comment didn’t make it to the proof. A year span between the design and actual production of the trusses didn’t help.
Mariachi’s guys worked all day on the repairs for the office room for about $675 plus the cost of some extra lumber. Not too shabby, all things considered.

Pro Tip: Keep all design change confirmations in a single, easily searchable location. Email threads and text messages can get buried quickly during construction. We learned this the hard way with our office ceiling height—a detail that got lost between design and execution despite being discussed months earlier.

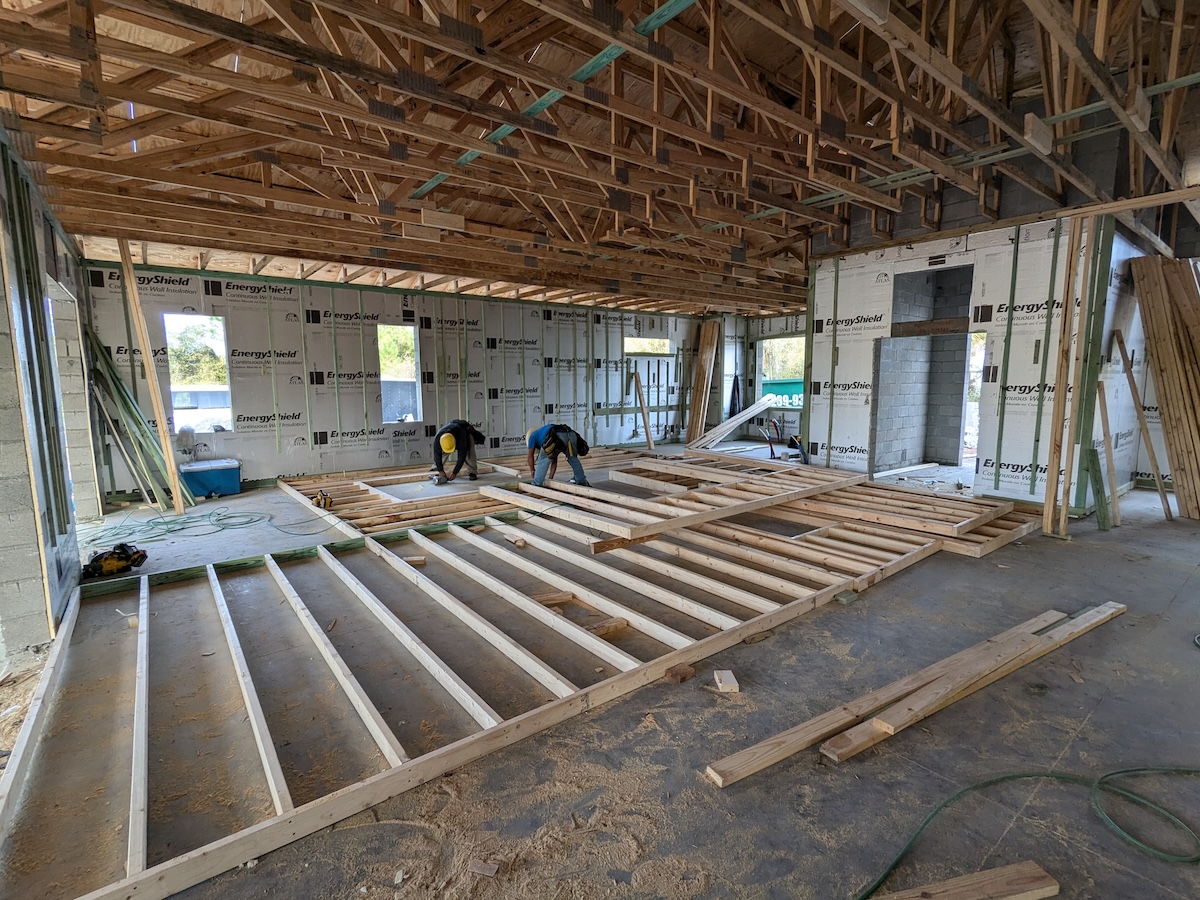
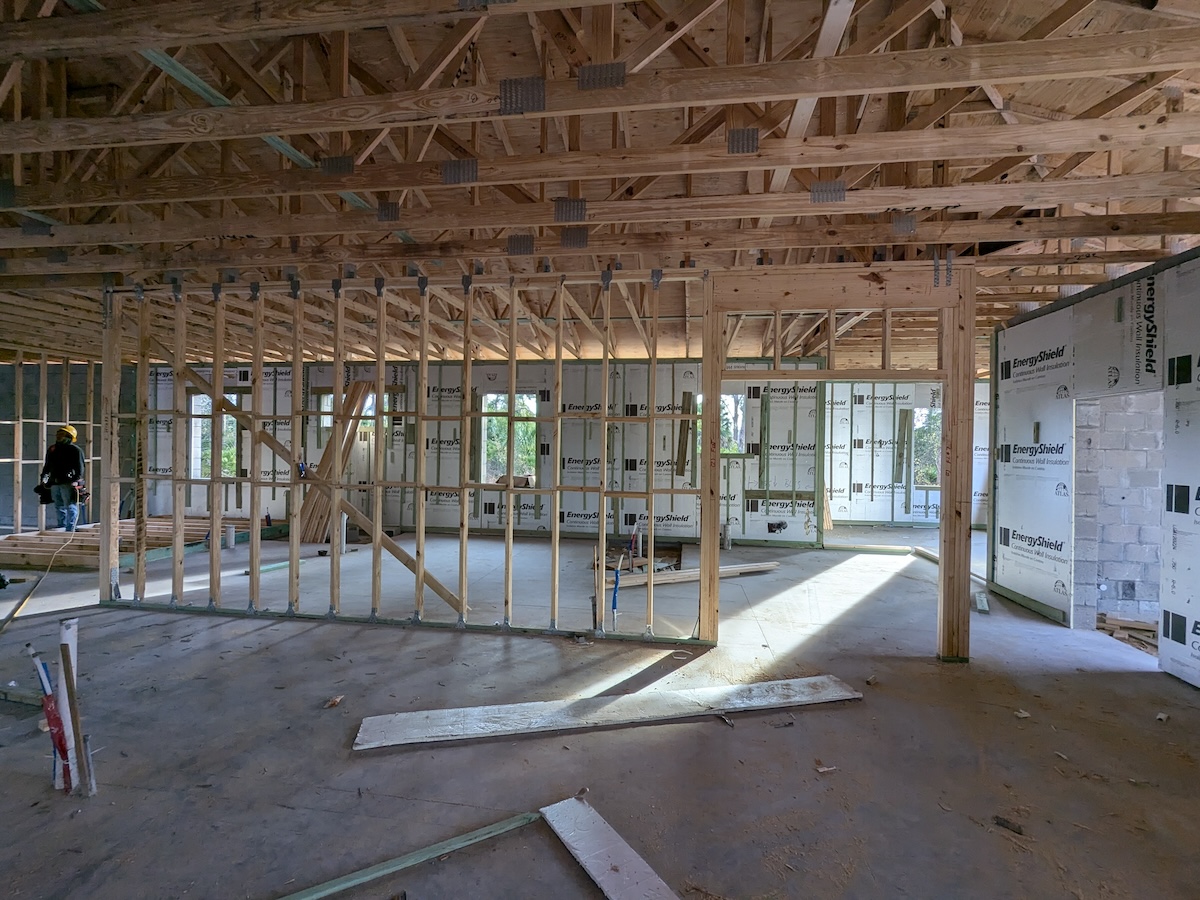
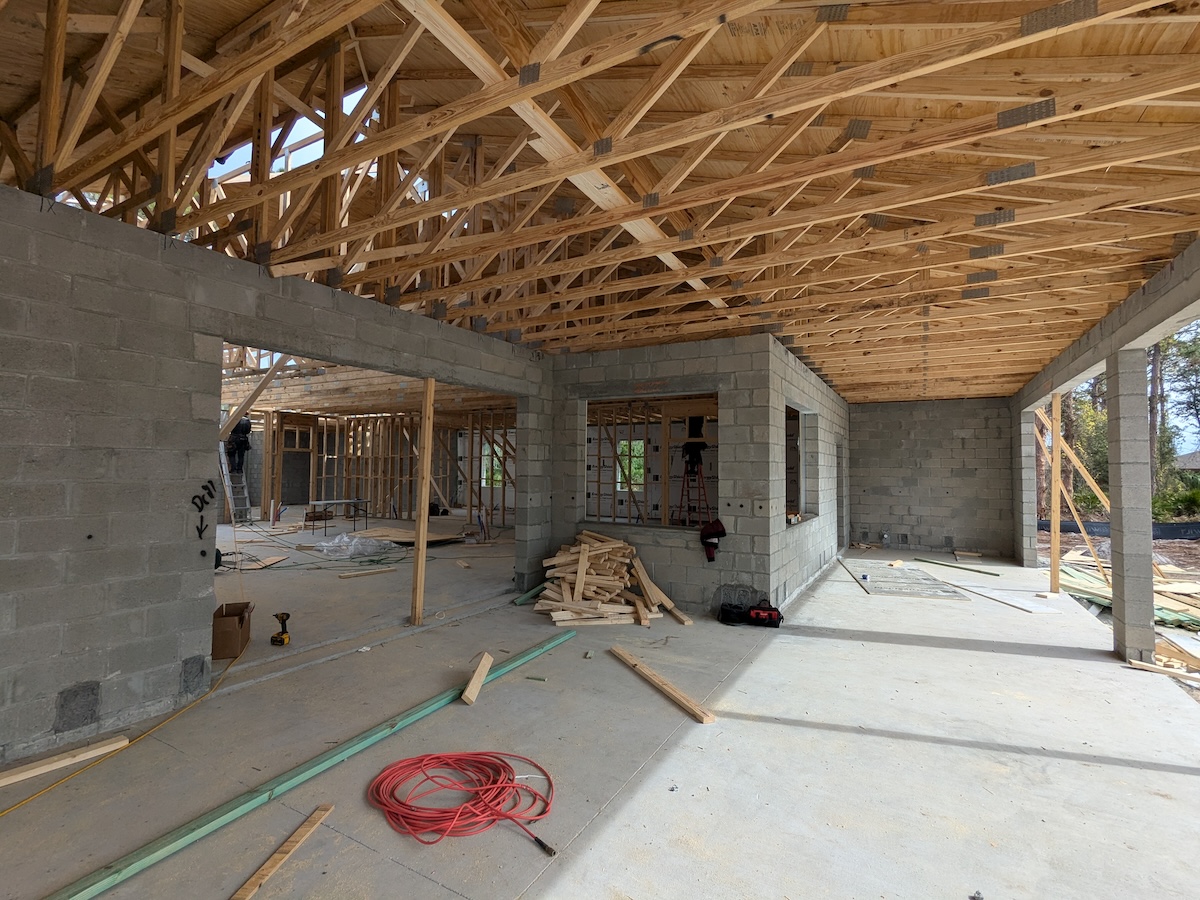
HVAC and Termite Control
After the walls were framed, we were able to start with the rough ins starting with the HVAC team. I also did a termite treatment with non-toxic borate on the 2x4s.
The HVAC guys knocked out their rough-in crazy fast—day and a half, tops. We did ask them to add another supply in the dining area because it just felt right. Little tweaks like that make all the difference.

Project Statistics Dashboard
Looking back, the transformation from December 2nd to the end of January is almost surreal. In just seven weeks, we went from bare earth to a fully enclosed structure with walls reaching to the sky and trusses spanning overhead. Even with my daily site visits, it’s hard to grasp how quickly skilled crews can turn concrete, blocks, and lumber into the bones of a home. Sure, there were hiccups along the way, but watching our “fortress” take shape in such a short time makes all the stress and constant site checks worth it.
Project Statistics Dashboard
Square Footage Analysis
Living Space (Conditioned)
Space Breakdown
Cost Comparison Analysis
Project Cost
January by the Numbers
Let’s talk money—because building a fortress isn’t cheap. January saw some significant expenses:
- Masonry and concrete work: $61,933 (including materials, labor, and management)
- Framing and lumber: $34,299
- Roofing (partial payment): $11,413
- Electrical materials and a few other big items in the same purchase: $5,998
- Other significant costs (garage doors, security, termite treatment, etc.): $8,400
Total January investment: $122,043
Project Cost Breakdown (as of January 2025) | ||
---|---|---|
Category | Line Item | Total Amount |
Architectural Fees | House Design | $4,450 |
Design-Related Deliverables | Blueprints Copies | $231 |
Professional Fees | Surveys, Energy Analysis, Reports | $7,186 |
Site Preparation | Land Clearing, Staking, Grading | $14,937 |
Permit Fees | City and County Permits | $5,829 |
Utility Fees | Water Meter Connection | $11,043 |
Construction Equipment | Generator | $748 |
Administrative Costs | Office Supplies, BuildBook, Security | $685 |
Framing | Truss Manufacturing, Lumber, Labor | $55,682 |
Doors and Windows | Windows, Doors, Installation | $52,636 |
General Conditions | Porta Potty, Dumpster, Site Services | $2,898 |
Foundation | Materials and Labor | $38,731 |
Masonry | Block Wall Materials and Labor | $43,733 |
Plumbing | Underground Plumbing | $5,560 |
Electrical | Materials | $5,998 |
Roof | Shingles and Underlayment | $11,413 |
Moisture Protection | Window Prep Materials | $744 |
Termite Treatments | Subterranean and Wood Treatment | $1,642 |
Selection Items | Exhaust Fans, Shower Faucets, Disposal | $1,622 |
Total Investment to Date | $300,819 |
Life Behind the Build
Building while maintaining family life feels like juggling flaming torches while riding a unicycle—blindfolded. Our garage has become a storage unit for construction supplies, forcing our car to brave the elements. Tatiana juggles homeschooling Yuna while managing Lina, who’s developed a remarkable talent for opposing everything (future lawyer, perhaps?).
Our legendary Sunday do-nothing days have become sacred, and hosting friends has taken a backseat to building our dream. But all of this should pass, and we can go back to showing off how retired we are. Hahaha.
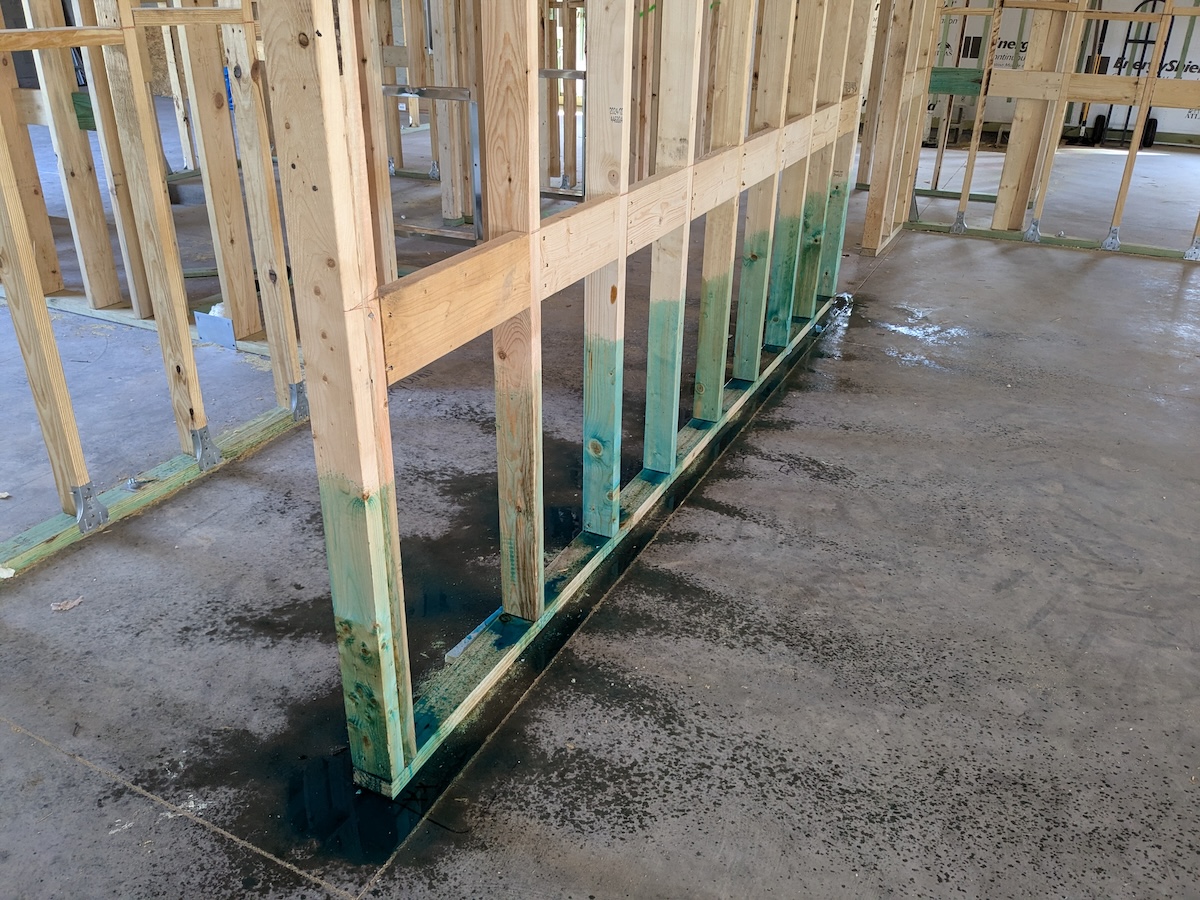
What’s Next? Racing Against the Florida Heat
Even though January was nuts, I could breathe a bit easier after the framing was done. The pace has slowed down some, but February’s going to be busy again. I’ll be helping the electrician with pulling the wires, and there’s plenty of sweat equity in my future. My days are getting longer as we try to make the most of daylight. I’m in a race against time to get as much done as possible before summer hits. I’m hoping to get electricity working by April and have a few fans on during the hottest hours of the day.
We’ve got a bunch lined up for February: finishing rough plumbing, starting electrical, getting those windows and doors in, finishing the roof shingles. After our big frame inspection, we can start insulating the attic and some interior walls to keep the noise down between rooms.
As far as running water, the city already installed our water meter! We’ve been using this crazy 700 ft hose running from a neighbor’s place! Once the plumber finishes the rough installation and we pass that inspection this month, we can start running our meter and ditch the long hose.
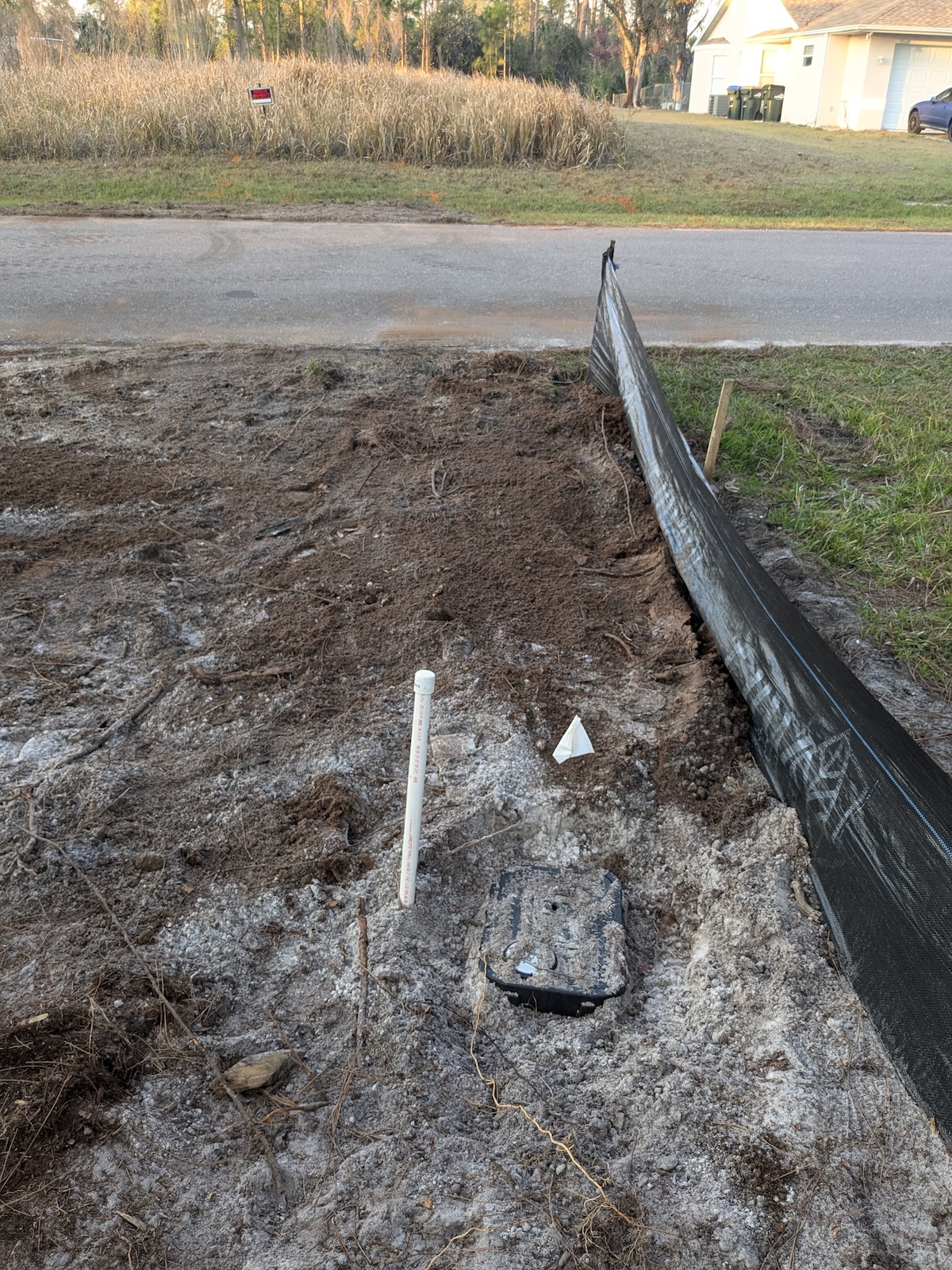
As we wrap up this January update, I can’t help but feel proud of how far we’ve come. From catching window spacing mishaps to redesigning our master bedroom entrance on the fly, every challenge has taught us something new about this owner-builder journey. Sure, our garage looks like a hardware store exploded in it, and our “do-nothing Sundays” have become precious commodities, but watching our “effing fortress” take shape makes it all worthwhile. Between juggling site visits, homeschooling, and trying to keep our sanity intact, we’re learning that building a house is really about building a life–one concrete block and truss at a time.
Stay tuned for our February adventures as we race against the Florida heat to turn this shell into a home. And hey, maybe by the next update, we’ll finally be rid of that 700-foot hose! Until then, keep building those dreams, whether they’re made of concrete or not.
Building your own house is a wild ride, but man, seeing it come together is worth every headache. Got questions about how we’re doing this? Drop them below—I love talking about this stuff, and there’s always something new to share.
Upcoming: HVAC, plumbing and electrical rough, exterior window and door installations, and roof shingle installation