Part 3 of Our Owner-Builder FIRE Journey Series
Where did December go? Wow, this has truly been our busiest December since we worked corporate jobs. The amount we accomplished this month went way beyond my expectations on the home building front.
Breaking Ground and First Steps
Remember when we mentioned that we broke ground on 12/2/24? That Monday morning started with a message from my shell contractor saying the footer crew was on their way. There I was, not quite ready for the 7 AM wake-up call! In Florida’s winter months, I usually wait until it hits 70 degrees before heading outside—typically around 11 AM. But when you’re building a house, the crew doesn’t wait for your high maintenance body temperature to kick in.
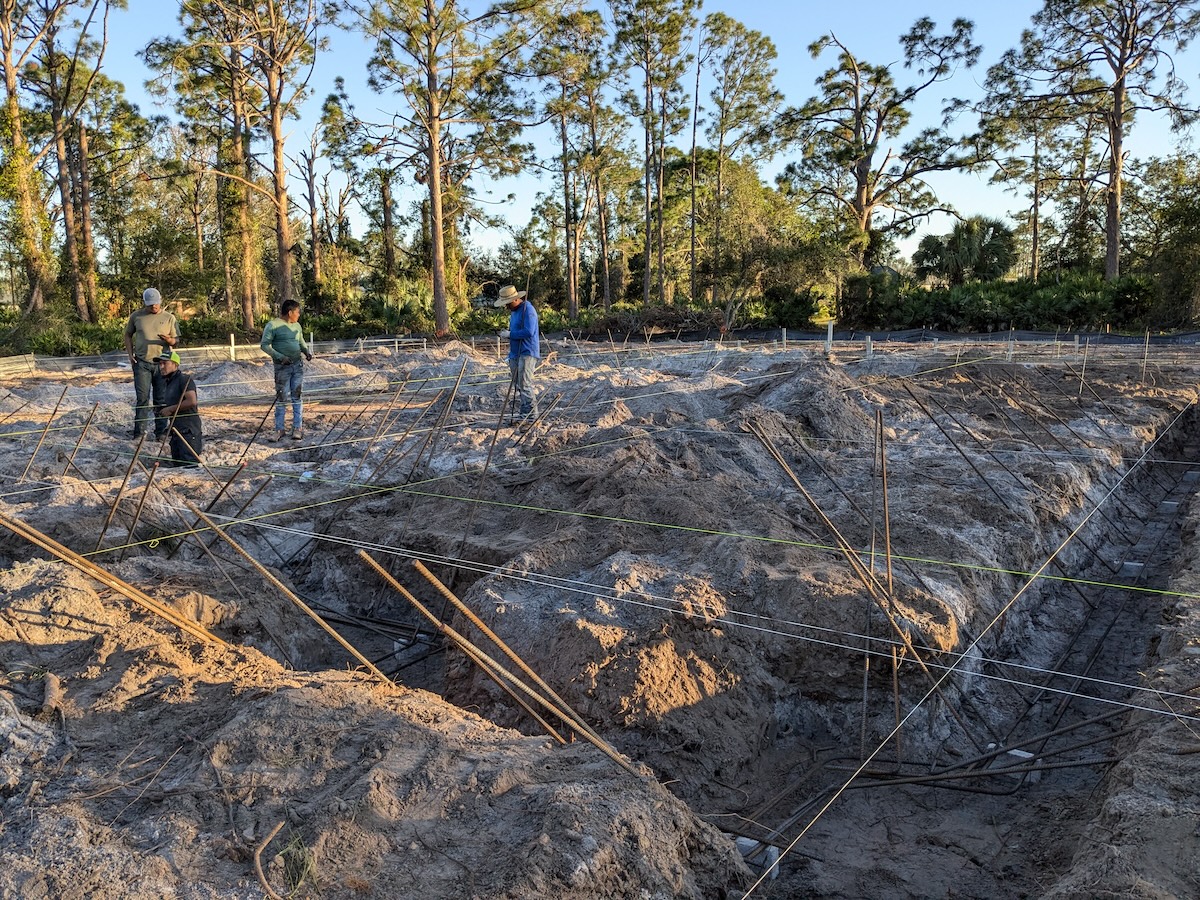
So what’s a footer, anyway? Think of it as the house’s foundation beneath the foundation. In Florida home construction, it’s a reinforced concrete base that supports the stem walls (those short walls that raise your house above ground level). The footer spreads the weight of your home across a wider area, crucial for our sandy Florida soil.
The Early Days Challenge: Racing Against Time
As we moved forward, those first few days tested our project management skills. We needed three critical inspections:
- Soil erosion (checking the silt fence)
- Tree removal verification
- Footer inspection
Here’s where it got tricky: we needed the first two inspections passed by 3 PM Tuesday to schedule the footer inspection for Wednesday. Why such a rush? Our footer pour had to happen Thursday, or we’d lose the crew for a week. In construction, missing your slot with a crew can set you back days or even weeks since their schedules fill up fast.
Pro Tip: When scheduling concrete trucks, flexibility isn’t really an option. Unlike other contractors, concrete companies run on tight schedules, especially in growing areas like ours. Why? Concrete has a limited window before it starts setting, and trucks can’t just wait around.
December’s Major Milestones
December turned into a month of incredible progress. We:
- Completed the footer pour
- Built the stem walls
- Installed underground plumbing
- Laid the groundwork for electrical
- Poured the slab
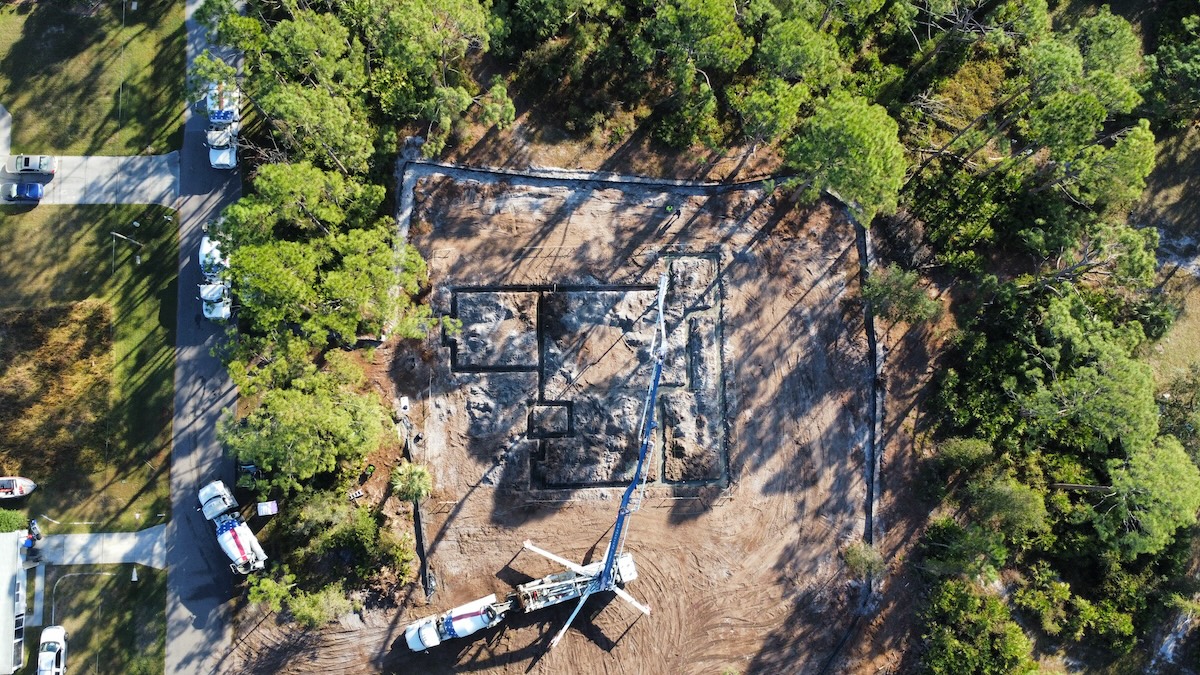
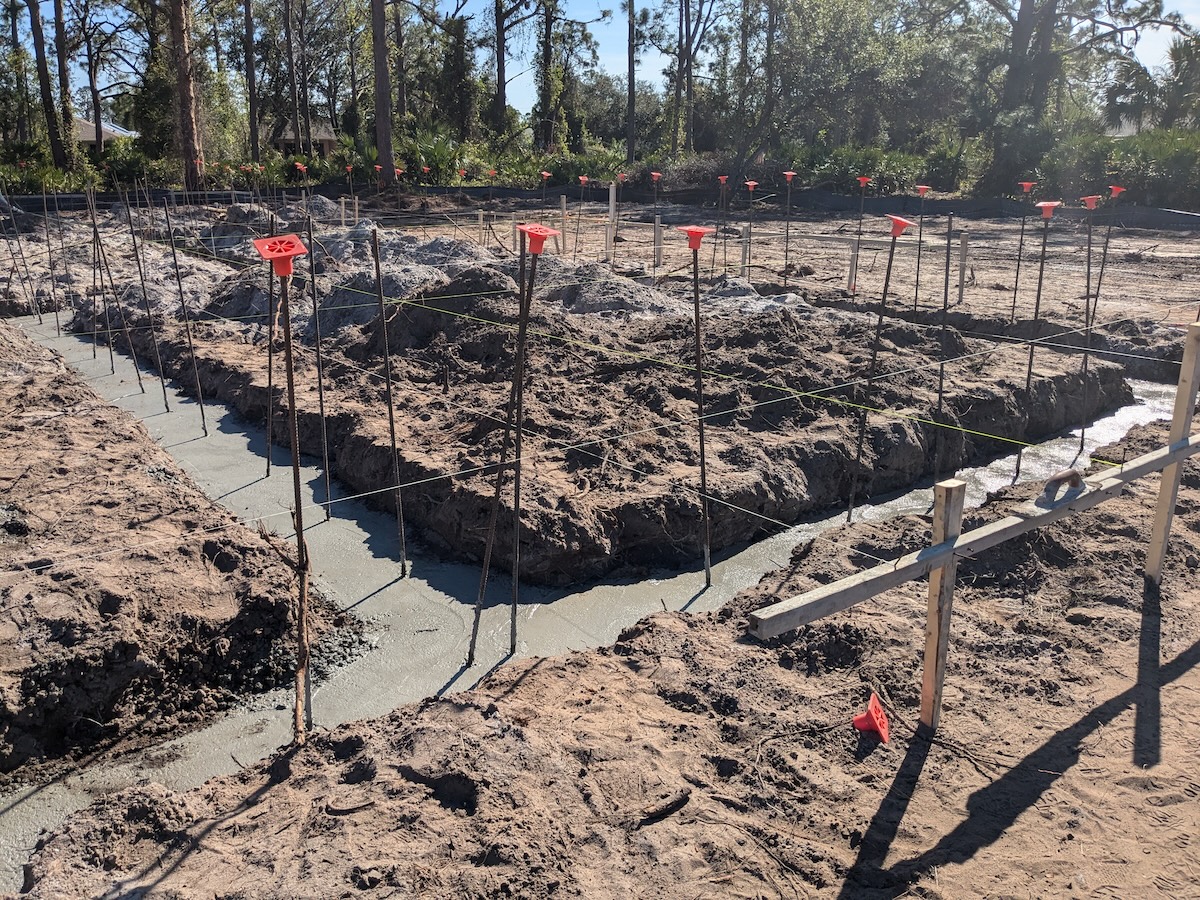
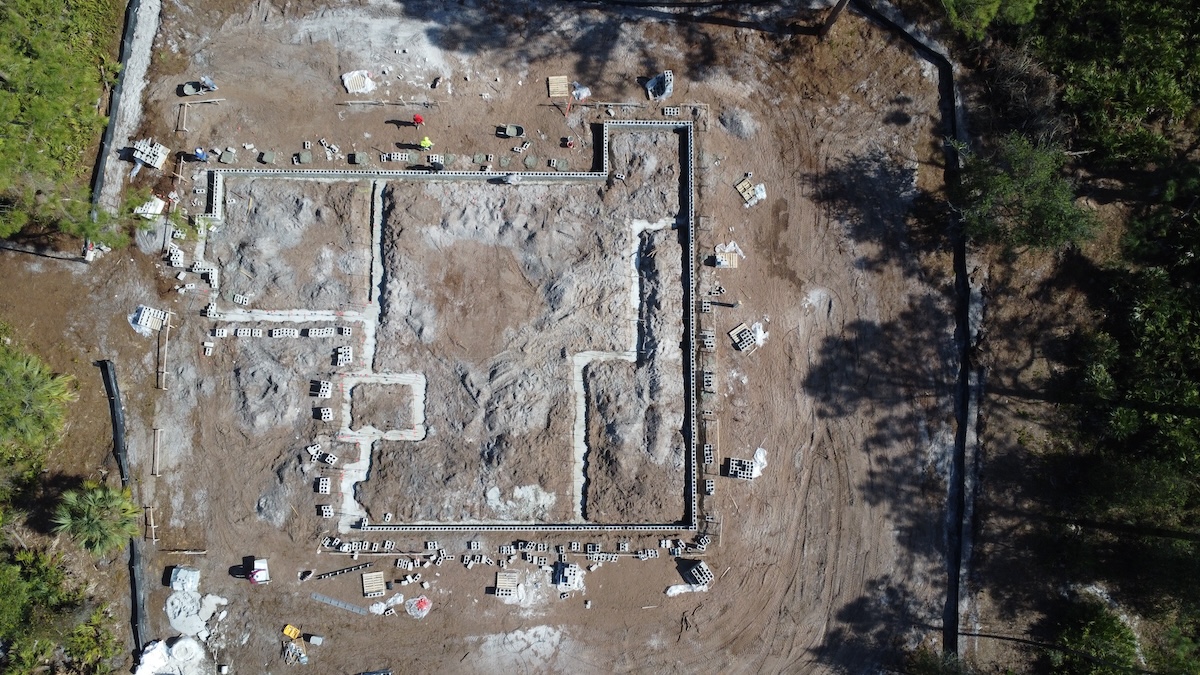
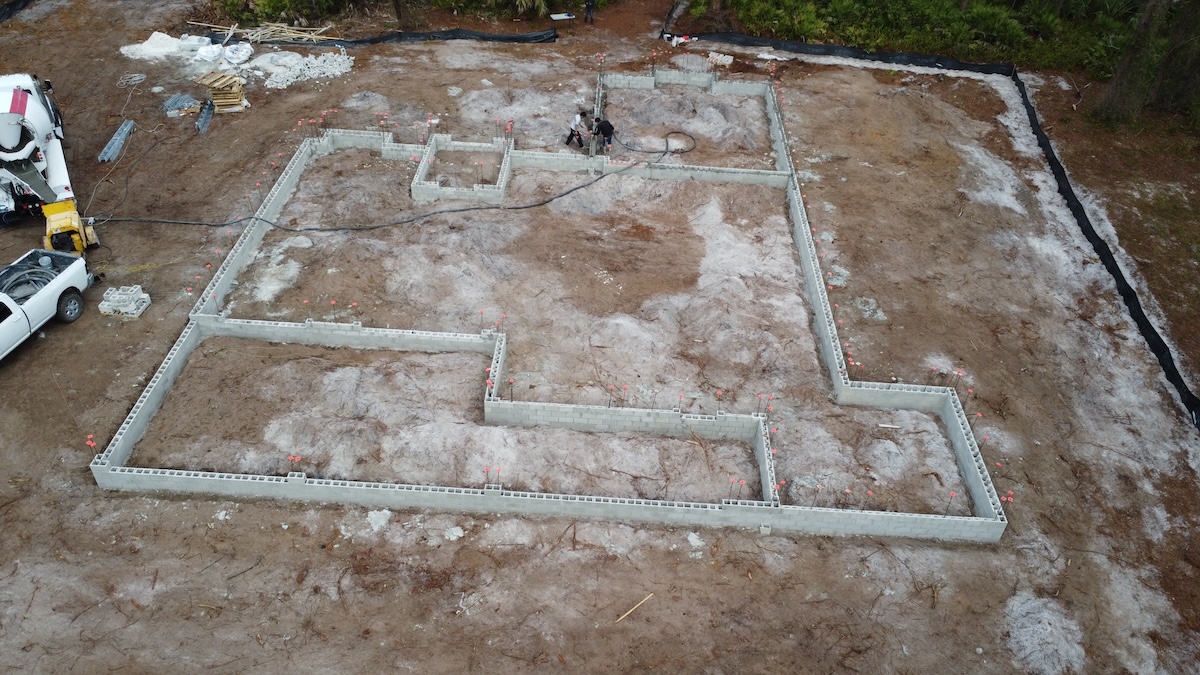
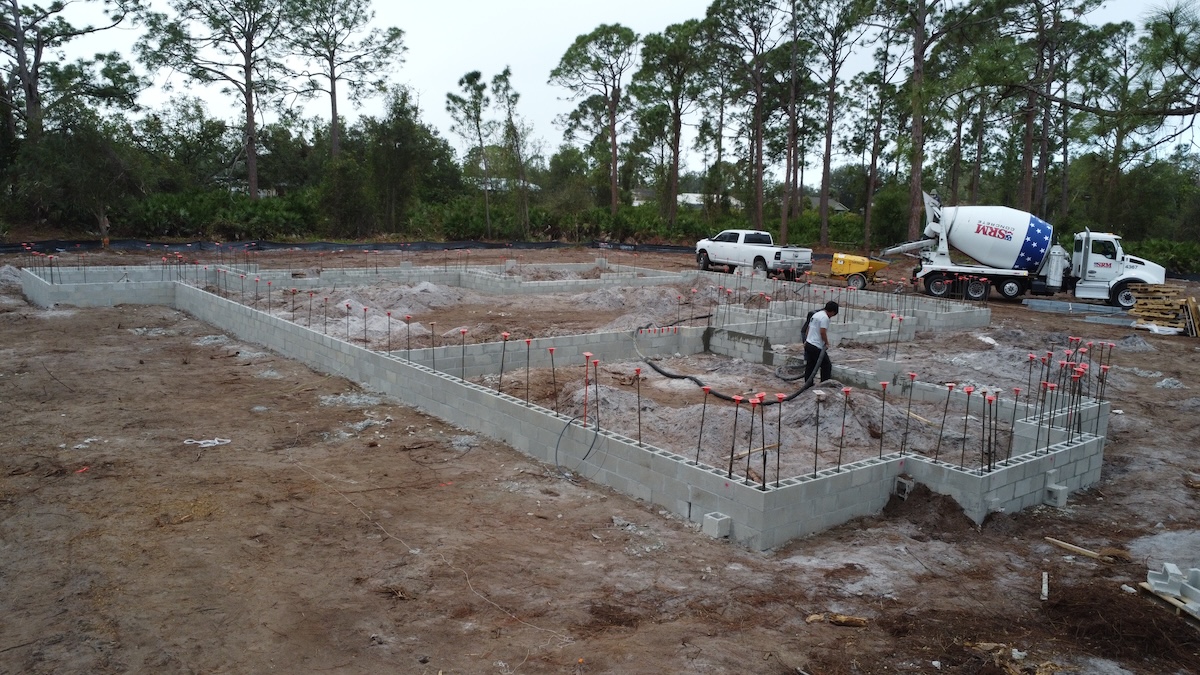
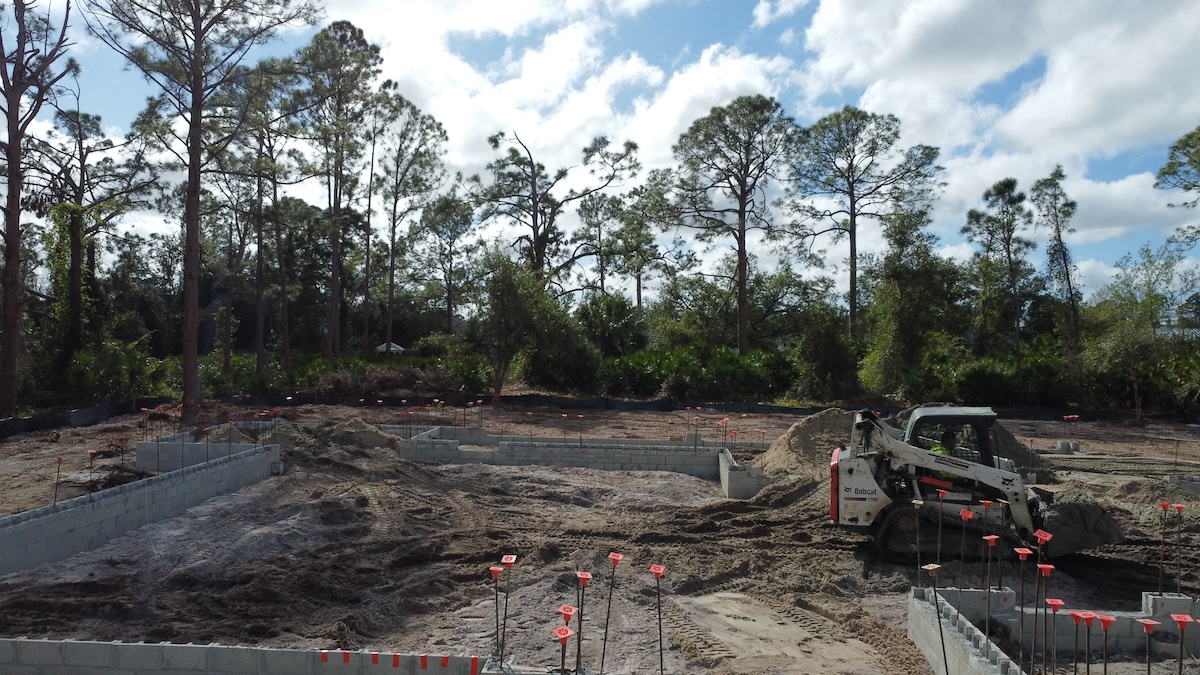
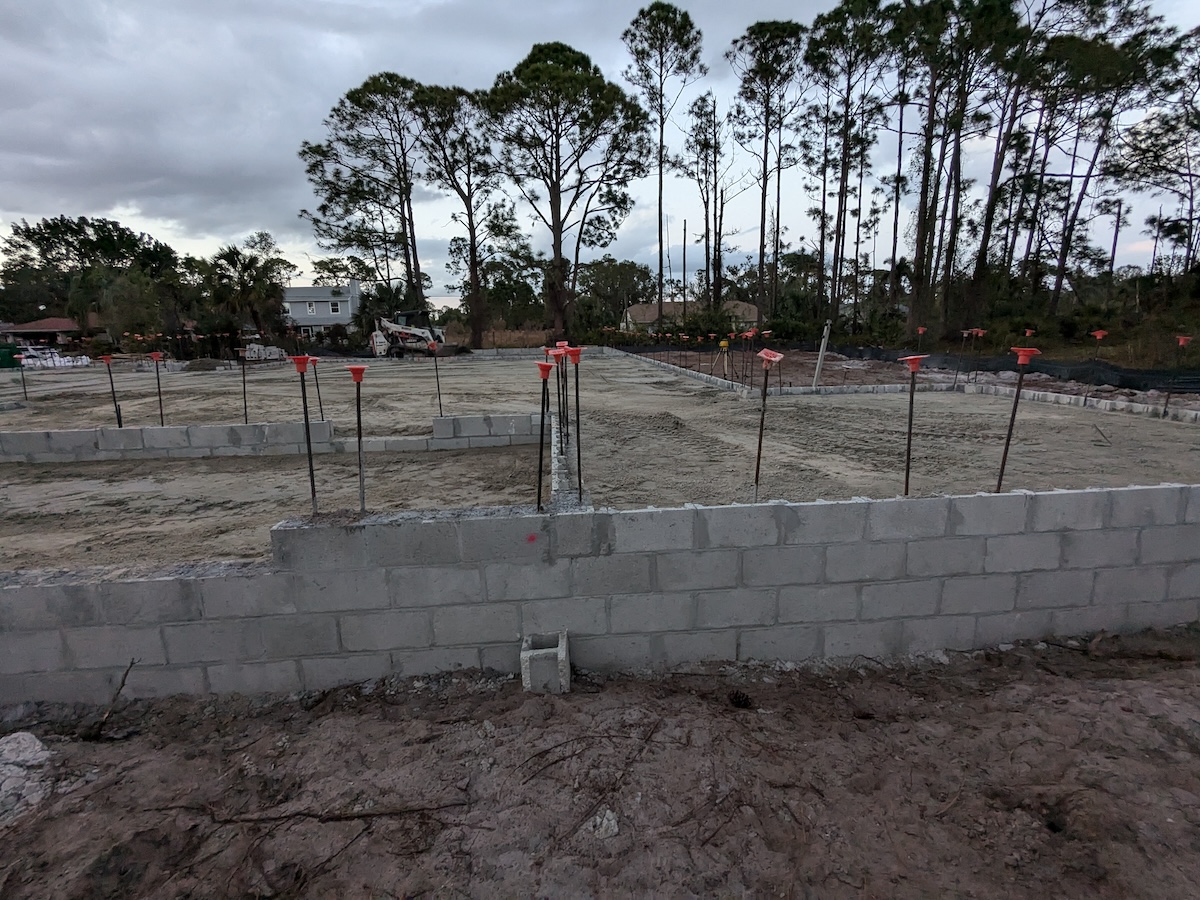
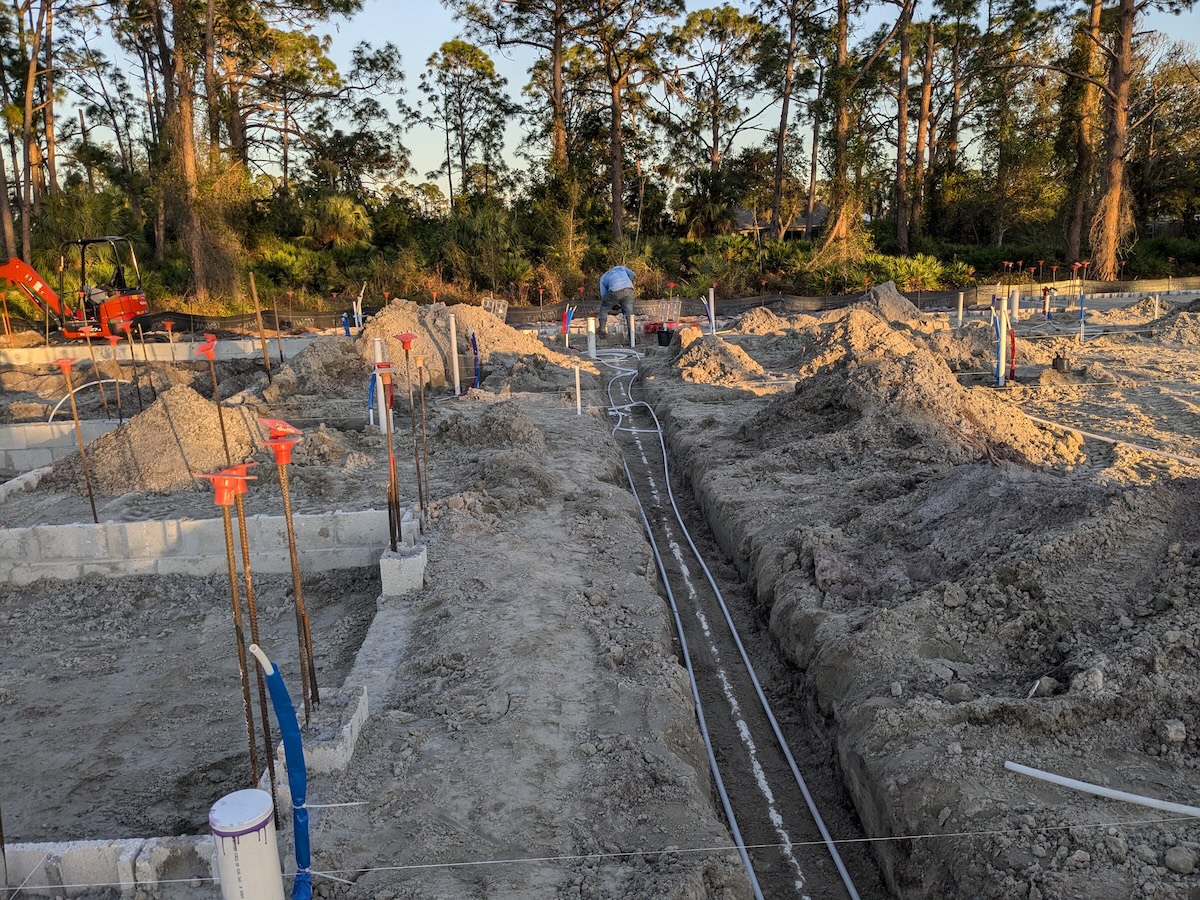
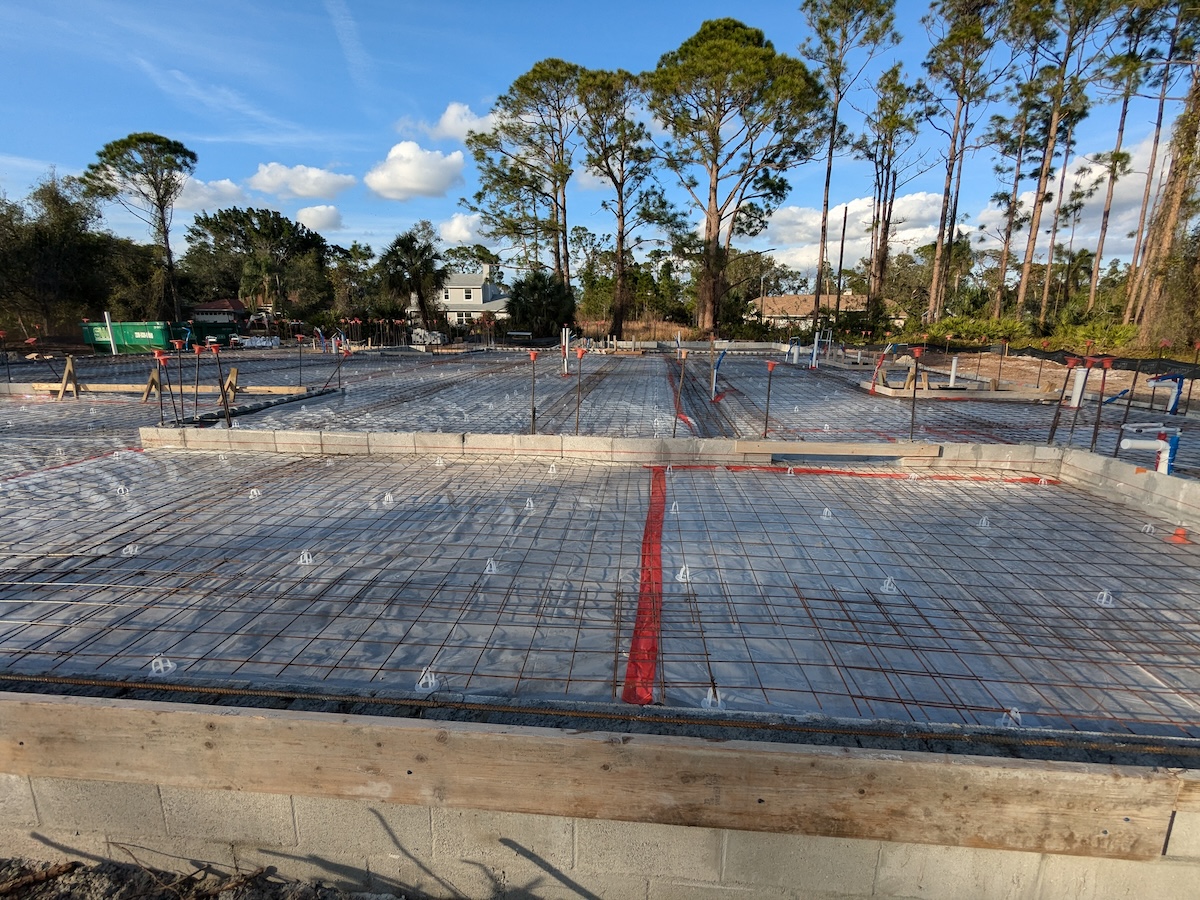
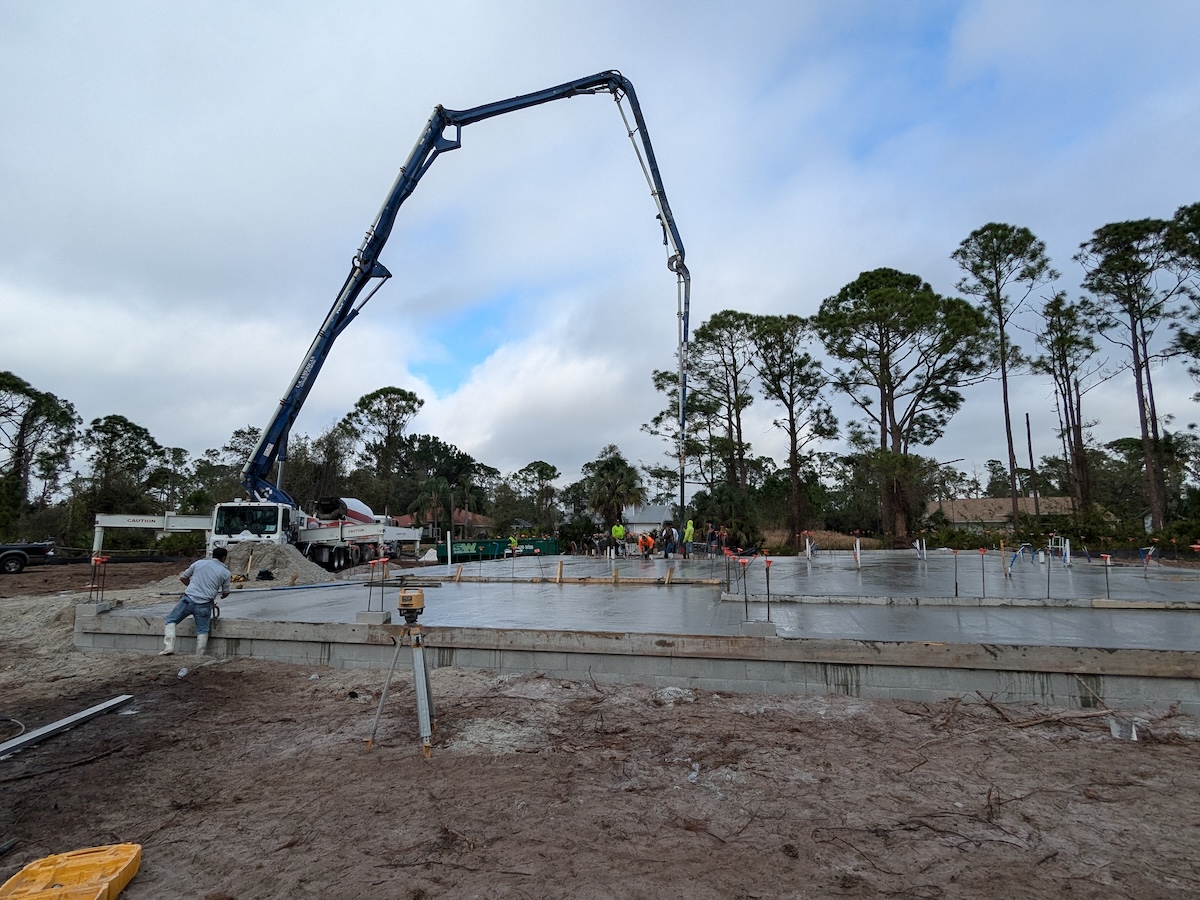
The slab pour on December 31st was particularly memorable—72 yards of concrete from 8 trucks! The cool morning weather worked in our favor. When pouring concrete in Florida, temperature matters big time. Hot, sunny weather makes the concrete set faster, giving crews less time to finish it properly. Our mild morning meant the crew could take their time getting everything just right.
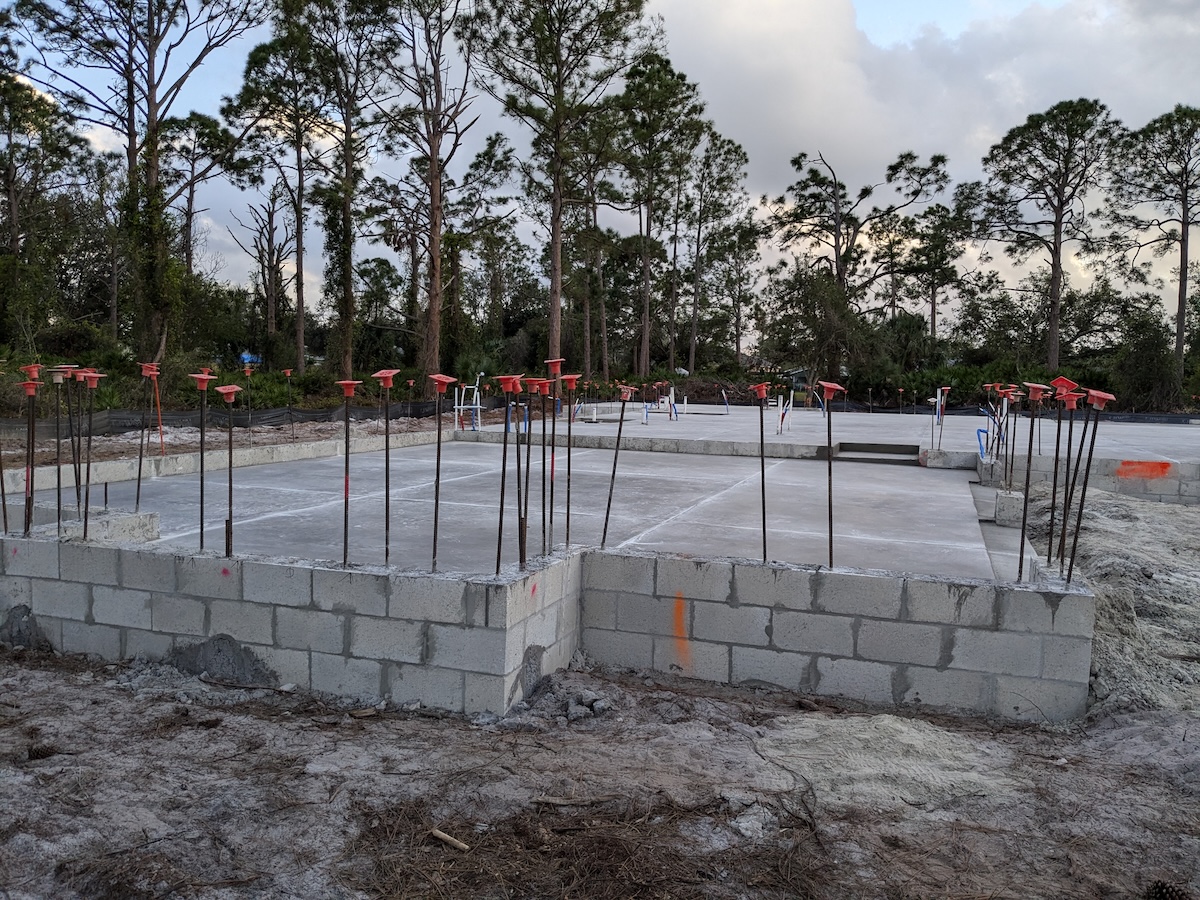
Building a Stronger Foundation
Want to know what sets our foundation apart from typical production homes? While most builders use fiber mesh or standard residential wire mesh, we opted for commercial-grade wire mesh in our slab. Why does this matter? Think of it like reinforcing a cardboard box with either regular tape or heavy-duty packaging tape. The commercial-grade mesh creates a significantly stronger foundation that can better handle Florida’s unique soil conditions and weather challenges.
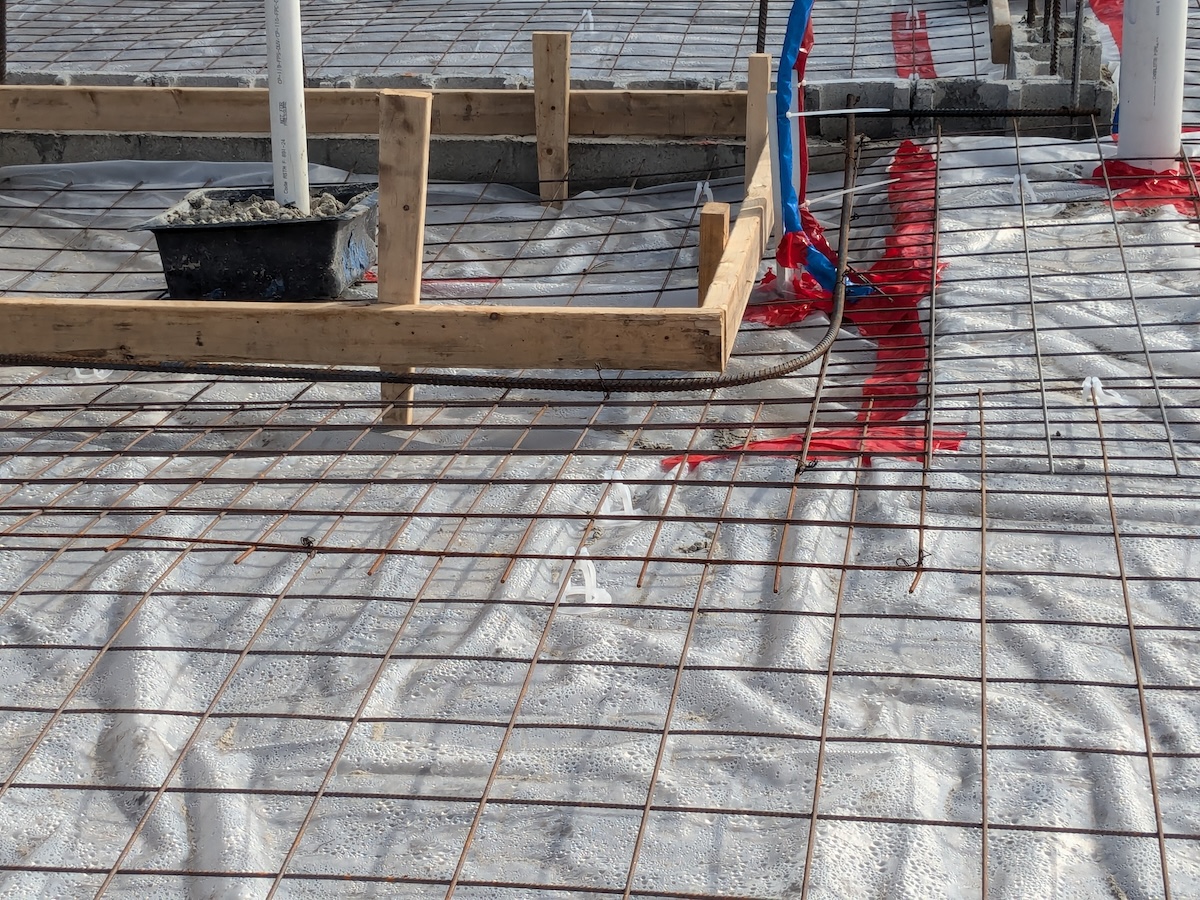
But a strong foundation isn’t just about the mesh. We built our home on a stem wall foundation rather than a monolithic slab. What’s the difference? A stem wall foundation raises the house slightly above ground level and provides better protection against hurricanes. Even though flooding isn’t common in our area, this design gives us extra peace of mind during heavy Florida rains.
This reinforced foundation approach might cost a bit more upfront, but it’s one of those invisible investments that pays off in the long run. After all, everything else in your home depends on having a rock-solid foundation!
Project Statistics Dashboard
Moving on to the numbers, let’s dive into our December stats—and wow, what a story they tell! In just 40 days since breaking ground, we’ve invested enough to bring our cost per square foot to $60.79. Now, before anyone gets sticker shock, remember that our area’s median listing price is $225 per square foot. We’re still coming in at about a quarter of the market rate, even with all our custom features.
Speaking of features, seeing our 2,941 square feet of living space take shape has been incredible. Each space now has real footings and foundation—it’s not just numbers on paper anymore! The 991-square-foot lanai might seem enormous (it is!), but that’s exactly what we wanted. In Florida’s climate, a lanai isn’t just a “nice to have”—it”‘s practically another living room. Plus, our 797-square-foot garage gives us plenty of room for two cars, beach and sporting gear, and projects.
What makes these numbers even more exciting is seeing how our careful planning is playing out in real life. That oversized pantry we dreamed about? It’s got foundation now. The bonus room that’ll serve as both guest space and homeschool central? We can actually stand where it will be. It’s amazing how a bunch of numbers on a dashboard can represent so much of our family’s future lifestyle.
Project Statistics Dashboard
Square Footage Analysis
Living Space (Conditioned)
Space Breakdown
Cost Comparison Analysis
Understanding Our Cost Analysis: Breaking Down the Numbers That Matter
Let’s talk about one of the most eye-opening aspects of our build: the cost per total square footage. This is the universal language builders speak when pricing homes, and it tells quite a story about our journey.
In the construction world, this metric includes everything under the roof: living space, garage, and yes, that spectacular lanai we’re building. It’s how builders calculate their base costs and, ultimately, what you’ll pay. But here’s where it gets interesting: notably, when we started getting quotes, one custom builder came in at $160 per square foot, with an additional $33,000 in non-construction fees, which typically include permit fees, site surveys, and land clearing expenses for an oversized lot like ours.
Do the math with our 4,729 total square feet at $167 per SF including the additional fees, and we would have been looking at a whopping $789,743!
Now, let’s talk about what “custom” really means in these situations. When most builders say “custom,” they’re really offering what I call “custom-lite”—you can pick from their pre-designed floor plans and make some modifications. Want to move a wall? Sure. Change some finishes? No problem. But true custom design? That’s usually not on the menu. And here’s the kicker: their quote didn’t even include the stem wall foundation we knew our house needed.
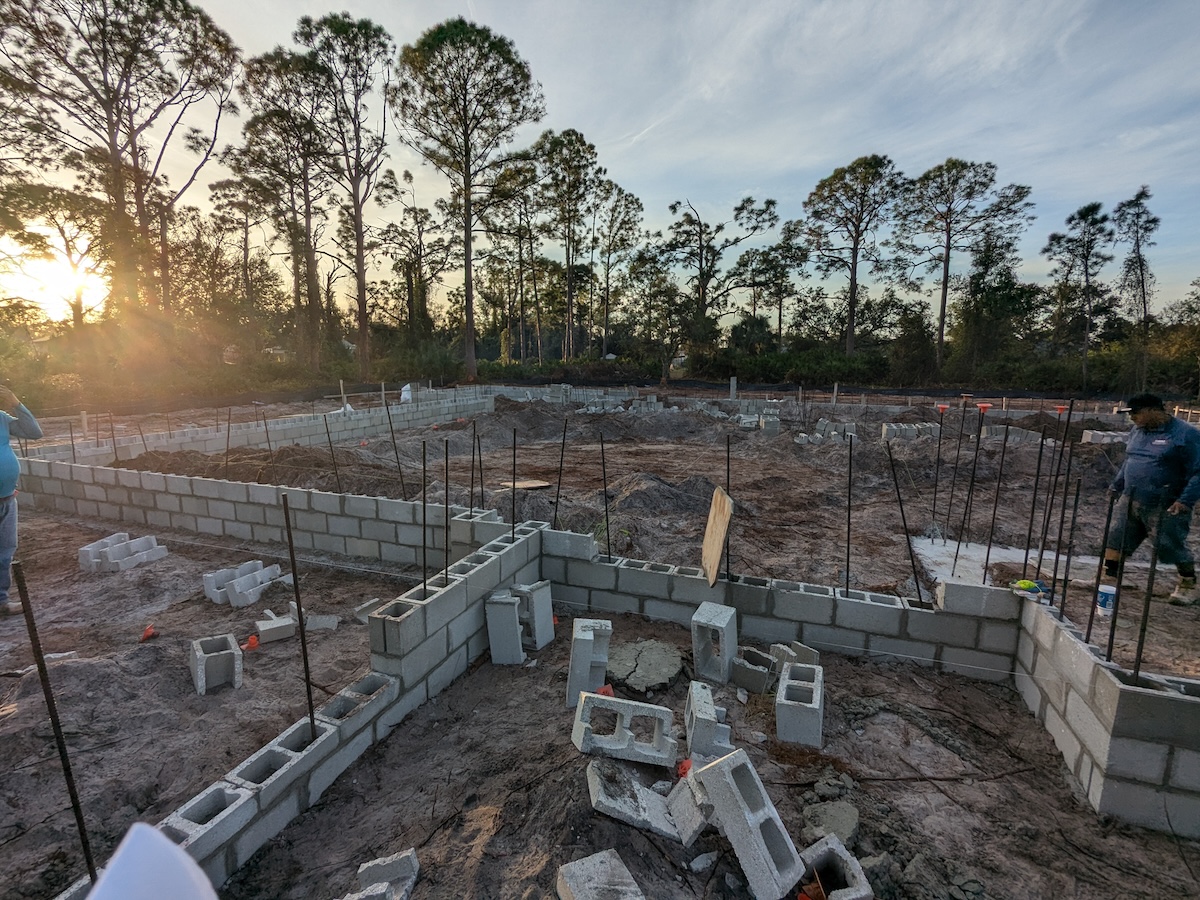
This is where our owner-builder journey really shines: our current cost per square foot is sitting at $37.80. Yes, you read that right—less than a quarter of that initial quote! And remember, we’re not cutting corners here. We’re actually going above and beyond with features like commercial-grade wire mesh in our slab and that robust stem wall foundation I mentioned earlier.
A Regional Reality Check: Understanding Market Rates
For context, custom homes in Southwest Florida typically run anywhere from $150 to $400 per square foot, depending on how luxurious you want to go. These prices usually reflect things like premium finishes, architectural complexity, and high-end features. But here’s what we’ve learned: being hands-on owners doesn’t just save money—it lets us invest in the things that really matter to our family while still keeping costs remarkably low.
The best part? We’re getting exactly what we want, not what a builder thinks we should have. Every dollar saved is a dollar we can put toward making this house truly ours, from that oversized pantry to the perfectly planned homeschool space. It’s about building smarter, not cheaper.
Project Cost
In terms of finances, our December spending reflected the intensive construction phase we’re in. Remember how I mentioned saving 20% on materials by ordering them directly? That decision can save us about $16,600 on our $83,000 materials order. Plus, using our credit cards can earn us $1,660 in cash back (2% rewards).
Project Cost Breakdown (as of December 2024) | ||
---|---|---|
Category | Line Item | Total Amount |
Architectural Fees | House Design | $4,450 |
Design-Related Deliverables | Blueprints Copies | $231 |
Professional Fees | Surveys, Energy Analysis, Reports | $6,336 |
Site Preparation | Land Clearing, Staking, Brushmowing | $15,912 |
Permit Fees | City and County Permits | $5,829 |
Utility Fees | Water Meter Connection | $11,043 |
Construction Equipment | Generator | $748 |
Administrative Costs | Office Supplies | $328 |
Framing | Truss Manufacturing | $23,193 |
Doors and Windows | PGT Windows, Sliding Glass Doors, Front/Back Doors, Installation | $48,673 |
General Conditions | Porta Potty, Water Connection, Dumpster, Clean-up | $1,517 |
Foundation | Materials, Labor, Treatment | $41,271 |
Plumbing | Initial Plumbing Work | $5,560 |
Masonry | Block Wall Material and Labor | $13,580 |
Selection Items | Garbage Disposal | $105 |
Total Investment to Date | $178,776 |
Strategic Decisions: Window Installation
Speaking of important decisions, here’s one worth sharing: we’re having our window supplier handle the installation. Why? Well, some of these windows are massive, and window installation isn’t something you want to get wrong. We could save some money doing it ourselves or hiring a separate contractor, but here’s my thinking: when the same company that sells you the windows also installs them, you get their full installation warranty. Plus, if anything breaks during installation (and with big impact windows, that could be expensive), it’s on them.
It’s like the difference between building your own computer versus buying one with a warranty–sometimes the peace of mind is worth the extra cost. After all, these are hurricane impact windows that need precise installation to perform properly during storms.
This approach also fits with one of our core building principles: know when to DIY and know when to let the experts handle it. Some things are worth paying extra for, and proper window installation in a Florida home is definitely one of them.
Some strategic wins:
- Working directly with vendors saved significant markup costs
- Using AI to compare vendor quotes helped optimize purchasing
- Building strong relationships with contractors led to better service and pricing
The Devil’s in the Details
Throughout this process, building a custom home means staying vigilant. No one knows your plans better than you do. A few examples of catches we made:
- Missing hose bib on one side
- Forgotten HVAC condenser pipes (caught this just before the slab pour!)
- Missed step-down in the laundry room entrance
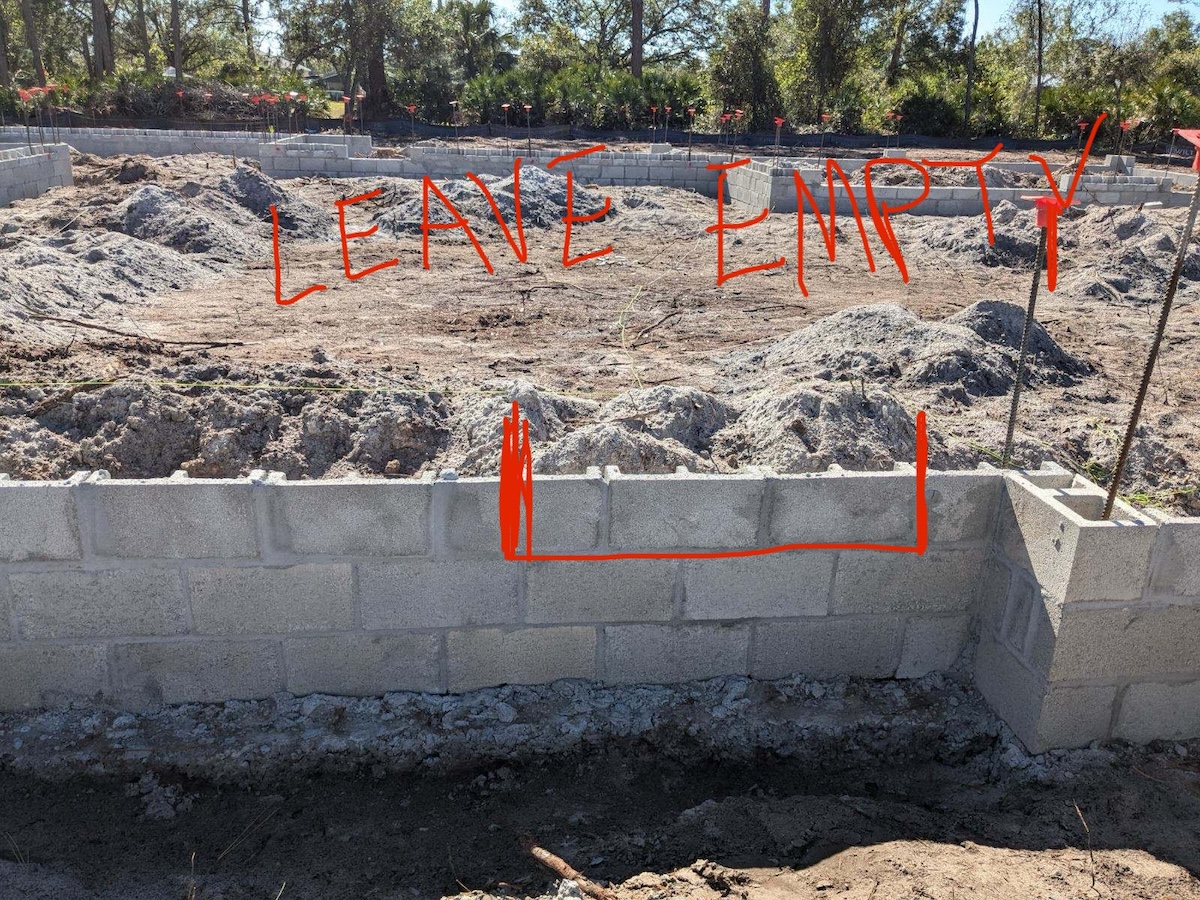
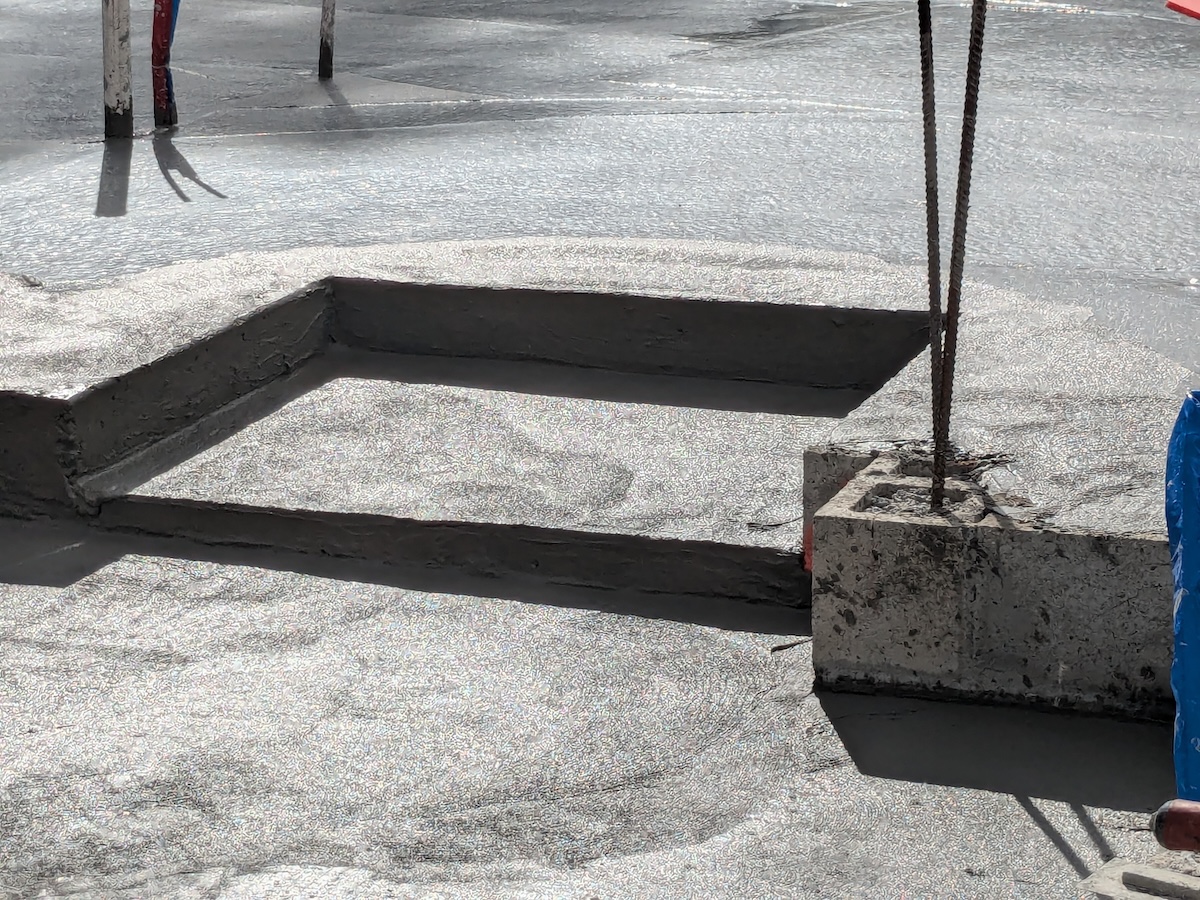
Why do these things get missed? Simple—most crews are used to building cookie-cutter production homes. Custom features require extra attention, and that’s where being an involved owner-builder really pays off.
Life Behind the Build
Meanwhile, going into full-time home-building mode has completely changed our daily rhythm. Some days start at 6 AM with material deliveries; others involve hunting down inspectors who haven’t shown up by noon. (Seriously, city planning department, a simple AM/PM window would be amazing!)
Tatiana’s picking up more household duties to keep things running smoothly. Thankfully, Lina being more independent now—potty-trained and vocal about her needs—makes things easier than if we’d started this a year ago. Yuna’s found her own way to participate, joining me for morning site visits and enjoying occasional sleepovers at grandma’s.
The best part? We’ve already cleared 13 out of 32 inspections! That’s more than a third of the way there. Yes, making weekday plans is tricky right now, but seeing our dream home take shape makes it all worthwhile.
Looking Ahead to January
As we enter the new year, we’re not slowing down! January’s agenda includes:
- Building block walls
- Interior wood framing
- Truss installation
If all goes well, we should be close to “dry-in” condition by month’s end. For those wondering, “dry-in” means the house has a roof, windows, and doors installed—basically, it’s protected from the elements. It’s a huge milestone in any build.
Want to follow our journey or plan your own build? Drop a comment below! I’d love to hear your thoughts or answer any questions about our owner-builder adventure.
Upcoming: Walls, Trusses, and Racing to Dry-In